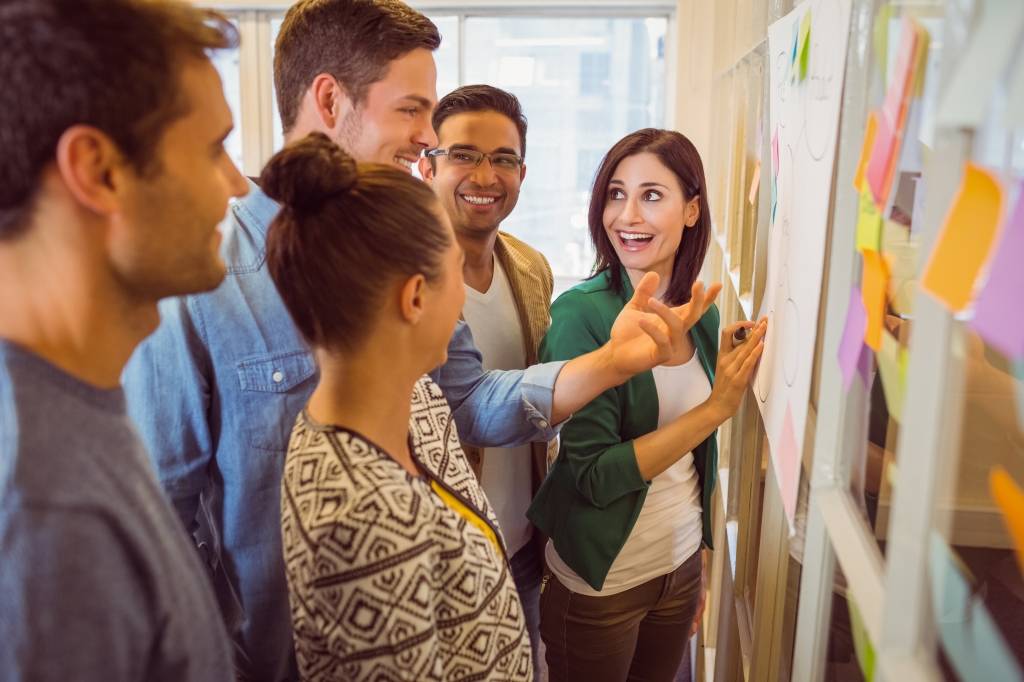
What is Kaizen Event?
‘Kaizen Event’ is a focused and structured continuous improvement project, using a dedicated cross-functional team to address a targeted work area to achieve specific goals in an accelerated time frame (usually 1 week or shorter) [1, 2, 3, 4]. In layman’s terms, a Kaizen event is an intensive and short-term project where employees of different organizational branches work together to implement actions to enhance and improve an existing process [5].
‘Kaizen’ in Kaizen Event is a Japanese word where ‘Kai’ means ‘change/improvement’ and ‘Zen’ means ‘for the better/good’ which can be roughly interpreted as “change for the better”. Here, Kaizen advocates a philosophy to work which is ‘Continuous Improvement’ that focuses on implementing small, incremental changes to obtain long-term and continuous improvements within processes with the involvement of employees in an organization [2, 4, 5]. Therefore, Kaizen Event is a method that works to realize this philosophy.
Aim & Purpose
The purpose of a Kaizen event is to carry out change and achieve goals in the work environment by improving processes, increasing efficiency, reducing waste, and developing people within an organization through low-cost solutions and Lean techniques [1, 4, 6]. These events bring together cross-functional teams – including operators, managers, and even owners – to determine and focus on a specific problem or issue within their operations and collaborate to identify process gaps, waste, or quality concerns as well as implement improvements in a short period of time, typically in a span of 3 to 5 days [1].
Along with that, the goal is to create rapid and substantial change through the collective effort and creativity of the team. Kaizen events aim to foster a culture of continuous improvement and empower employees to take ownership of their work, develop themselves, and make positive changes in their workplace [3, 6]. Ultimately, the purpose of a Kaizen event is to drive measurable results and create a lasting and significant impact on the organization.
Additionally, Kaizen events can also be referred to as “rapid improvement events”, “Kaizen blitz”, “process improvement projects”, “waste elimination workshops”, and “accelerated improvement workshops” [6] which all have similar concepts and practices involving efforts to improve processes and achieve goals within a short period of time.
Benefits of Implementing Kaizen Event in Your Organization
So why do I need to start implementing Kaizen Events in my organization? How could it be beneficial for my company and employees?
There are actually a plethora of benefits that you will gain from working together with your team to implement a Kaizen event in your organization. For many years now, implementing a Kaizen event has been gaining in popularity among many organizations as it works as an organizational improvement method that has given positive impacts on their business in transforming and developing their working environment and employees [1]. Below is a list of these benefits [1, 5, 6, 7];
- A low-cost rapid improvement method
- Provide a systematic and holistic project environment
- Provide a structured problem-solving process
- Provide rapid improvement in a short period of time
- Reduce cost and enhance profitability
- Reduce work-in-process/inventory levels
- Enhance lead time/cycle time
- Helps employees of different branches enhance their awareness and understanding of the flow and impact of the processes on their and others’ works
- Increase productivity and efficiency
- Increase employee’s problem-solving skills
- Reduce the number of defect rate/quality issues
- Increase innovation and creativity
- Encourage the need for change, improvement and employee engagement
- Empower employees
- Enhance internal team processes, communication, and teamwork among employees of different branches
- Fostering a change in organizational culture that focuses on continuous improvement and achieving long-term improvement
When Should You Implement Kaizen Event in Your Organization
We now know that Kaizen events bring a significant and positive impact on organizations, but the question of ‘when is the right time to implement a Kaizen event?’ remains.
Well, the answer to that is that an organization can implement a Kaizen event at any time to optimize its processes continuously. However, since implementing this project requires your employees’ time and full commitment, it is more beneficial and convenient to do so when your organization is facing certain situations, for instance [8, 9]:
When an urgent issue arises and requires quick solutions
Issues can be quality problems (i.e., defects), high waste levels, frequent machine downtime, bottlenecks, etc. Implementing a Kaizen event can be an effective way to bring together people related to this issue to brainstorm, identify the root cause of the issue and come out with a quick and practical solution to rectify it.
When your organization is targeting specific goals/KPIs
Kaizen event is a practical way for you and your team to achieve goals or KPIs as it can help you measure and compare your current performance to your goals through documentation. Hence, you and your team can strategize a better and more efficient way to improve your current performance to achieve these goals.
When your daily processes are found inefficient and lagging behind competitors
If you find that the daily processes that your organization has been carrying out are slow and lagging behind your top competitors, implementing Kaizen events can help determine the cause of the problem and find the best solutions to make improvements in order to catch up with competitors in the long run. What’s more, through Kaizen events, your team and organization will likely build a ‘continuous improvement’ culture and be more active and involved to consistently find ways to make changes/improvements in processes throughout the organization.
When your organization requires cross-functional collaborations
When you work in a big company that requires collaboration with people from different departments, it tends to be difficult to work on a project head-on without first sorting out the work dynamics of the other departments’ employees that you are not familiar with.
That is why having a Kaizen event can be beneficial as it can help everyone involved to come together and collaborate to work on a common goal and enhances communication among workers of different departments. This is important so that each department representative can contribute effectively and a project can flow smoothly. In addition, since Kaizen events typically adopt common problem-solving methods like PDCA, it can act as a guide and a structured process for everyone involved to follow together.
How to Implement Kaizen Event
So how exactly does an organization implement a Kaizen event?
For starters, a Kaizen event typically uses a common problem-solving strategy that involves a number of phases such as;
- Defining the problem/issue that needs to be addressed during the event for improvement.
- Creating a team of 5 to 10 employees from different departments that are directly involved with the process or issue that needs improvement.
- Collecting and analyzing data on the current situation to identify the root cause of the problem and determine areas for improvement.
- Developing a detailed event plan (objectives, timeline, responsibilities, etc) and brainstorming possible action plans to rectify the issue and improve the process.
- Implementing, testing, and adjusting proposed action plans for process improvements through team collaboration.
- Monitoring the results and process performance regularly in order to sustain the achieved improvements over the long term.
- Sharing results of the event throughout the organization to encourage more continuous improvement implementations and promote a culture change to one that focuses on continuous improvement.
However, these steps may vary depending on the organization’s specific needs and goals. Hence, popular problem-solving methods like DMAIC (Define, Measure, Analyze, Improve & Control), PDCA (Plan, Do, Check & Act), and 8D (Eight Disciplines) are some of the methodologies that organizations choose to employ to implement Kaizen events.
These methodologies may have similar fundamental steps such as defining the problem, finding the root cause, generating solutions, executing solutions, and monitoring and sustaining, but they also have added steps or practices that can meet the specific needs of your organization. Also, Kaizen events often employ Lean tools such as SMED (Single-Minute Exchange of Die), VSM (Value Stream Mapping), 5S, etc. which are very effective to assist to improve and enhance processes.
What are The Characteristics of A Successful Kaizen Event?
Implementing a Kaizen event using popular methodologies and tools is not enough to ensure that your Kaizen event can be successful and show significant improvements in your processes. If your Kaizen event is implemented but lacks resources, no commitment from team members, or even poor and unorganized event planning, your Kaizen event may not show the results your organization is asking for.
To ensure a successful Kaizen event, it is highly recommended to have;
Clear objectives and the right approach
You and your team need to clearly define the objectives of the Kaizen event and have a structured, systematic approach to problem-solving – choosing the right problem-solving methodology to employ – in order to set a clear focus of the current situation, plan the right strategy, and be able to convert visions into clear-cut measurable targets that can be monitored after the event.
Active involvement of event team members
Also, it is of utmost importance that all of your team members are fully committed and actively involved in the event so that they can be more focused and critical on process improvement efforts and provide their expert opinions and suggestions to improve and resolve the issues at hand. Team members also need to develop effective communication so that they can help each other out with areas that one is not an expert in and can brainstorm effectively to make the right and best decisions to address the issues/problems.
Adequate resources
Additionally, your organization’s top management also needs to play a role in providing enough resources to prepare for the event and execute the action plans proposed (i.e., time, money, equipment, training, etc.) so that the improvement efforts can be realized effectively.
Open mind toward change
Finally, to foster a whole culture of continuous improvement after implementing a Kaizen event, everyone involved in the event needs to have an open mind toward changes in the operations/processes so that they can cooperate better with new ideas, adapt to new things and grow as a company.
To summarize, implementing a Kaizen event is a beneficial improvement project for your organization as it can effectively streamline and make rapid changes and improvements to your processes/services, transforming your organization to become more efficient, effective, and competitive.
Interested to implement the first Kaizen event for your organization? Hit us up!
f you are interested to implement the first Kaizen event in your organization but are still unsure of how to start or what tools to utilize, hiring third-party consultants who are experts in process improvement is a good way to start.
We, in MBizM Sdn. Bhd., are a certified and accredited training and consultancy provider specializing in Lean Six Sigma, quality and process improvement, consultancy, and coaching. Our certified full-time consultants – with years of experience in process improvement – can offer expert guidance to your Kaizen event team members to implement the event properly, help evaluate the current situation of your targeted processes, determine the best tools and approach to employ in the Kaizen event, and provide guidance to make the improvements sustainable in your organization.
Come and visit us at https://www.mbizm.com/ for more information, or you can fill in your details and inquiries at: https://www.mbizm.com/contact-us/ and we will help you get started.
Be a member today!
Join us and become a member at https://sixsigma.org.my/membership/ and receive various membership perks – vouchers, discounts, networking, and more! Visit us at https://sixsigma.org.my/ for more information.
Looking forward to having you onboard!
References
[1] B. Vo, E. Kongar, and M. F. Suárez Barraza, “Kaizen event approach: a case study in the packaging industry,” International Journal of productivity and performance management, vol. 68, no. 7, pp. 1343-1372, 2019.
[2] L. J. Cheng, (2018), “Implementing Six Sigma within Kaizen events, the experience of AIDC in Taiwan”, The TQM Journal, vol. 30, No. 1, pp. 43-53, 2018. https://doi.org/10.1108/TQM-02-2017-0017
[3] J. A. Farris, E. M. Van Aken, T. L. Doolen, and J. Worley, “Critical success factors for human resource outcomes in Kaizen events: An empirical study,” International journal of production economics, vol. 117, no. 1, pp. 42-65, 2009.
[4] J. A. Garza-Reyes, C. Christopoulos, A. Kumar, S. Luthra, F. González-Aleu, V. Kumar, and B. Villarreal, “Deploying Kaizen events in the manufacturing industry: an investigation into managerial factors,” Production Planning & Control, vol. 33, no. 5, pp. 427-449, 2022.
[5] P. Peterka, “Article: Making use of the Kaizen event in the Office,” SixSigma.us. https://www.6sigma.us/lean-six-sigma-articles/making-use-of-the-kaizen-event-in-the-office/ (accessed February 3, 2023).
[6] W. J. Glover, W. H. Liu, J. A. Farris, and E. M. Van Aken, “Characteristics of established kaizen event programs: an empirical study,” International Journal of Operations & Production Management, vol. 33, no. 9, pp. 1166-1201, 2013.
[7] L. R. Lina, and H. Ullah, “The concept and implementation of Kaizen in an organization,” Global Journal of Management and Business Research, vol. 19, no. 1, 9-17, 2019.
[8] D. Dolcemascolo, “Kaizen events: When and how to use them,” ReliablePlant. https://www.reliableplant.com/Read/8904/kaizen-events#:~:text=Kaizen%20events%20are%20traditionally%20short,the%20scope%20of%20the%20operators (accessed February 3, 2023).
[9] M. Banna, “When to use a Kaizen event vs. Daily kaizen,” KaiNexus. https://blog.kainexus.com/improvement-disciplines/kaizen/kaizen-events/when-to-use-a-kaizen-event (accessed February 14, 2023).